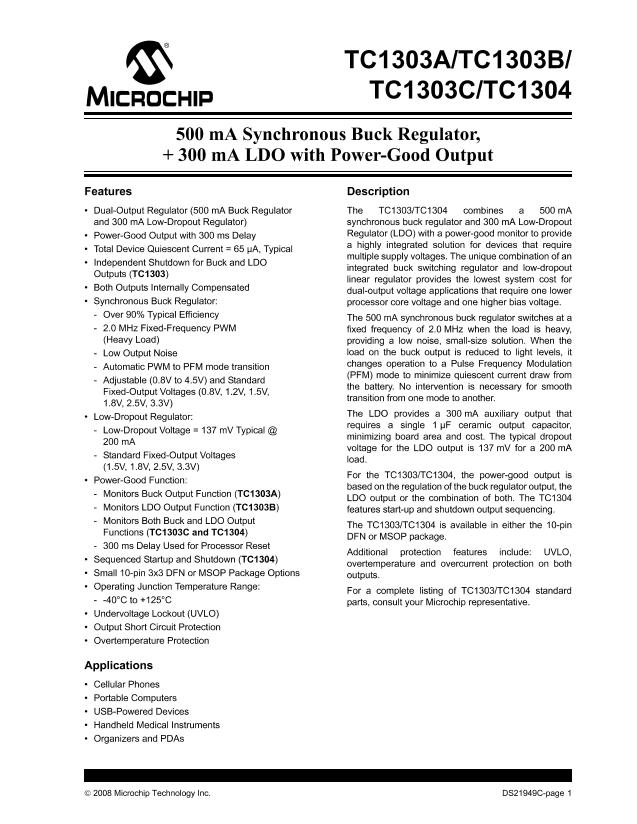
TC1303C-1A1EMF
Model | TC1303C-1A1EMF |
Description | 0.5 A SWITCHING REGULATOR, 2400 kHz SWITCHING FREQ-MAX, PDSO10, 3 X 3 MM, 0.9 MM HEIGHT, PLASTIC, DFN-10 |
PDF file | Total 38 pages (File size: 756K) |
Chip Manufacturer | MICROCHIP |

TC1303A/TC1303B/TC1303C/TC1304
5.5
Inductor Selection
TABLE 5-2:
For most applications, a 4.7 µH inductor is recom-
mended to minimize noise. There are many different
magnetic core materials and package options to select
from. That decision is based on size, cost and accept-
able radiated energy levels. Toroid and shielded ferrite
pot cores will have low radiated energy, but tend to be
larger and higher is cost. With a typical 2.0 MHz
switching frequency, the inductor ripple current can be
calculated based on the following formulas.
TC1303A, TC1303B, TC1303C,
TC1304 RECOMMENDED
INDUCTOR VALUES
DCR
MAX
Ω
I (A)
(MAX)
DC
0.091
0.108
0.154
0.075
0.104
0.118
0.116
0.174
0.216
0.35
0.11
Size
WxLxH (mm)
Part
Number
Value
(µH)
Coiltronics
®
SD10
SD10
SD10
Coiltronics
SD12
SD12
SD12
2.2
3.3
4.7
2.2
3.3
4.7
4.7
4.7
1.80 5.2, 5.2, 1.2 max.
1.42 5.2, 5.2, 1.2 max.
1.29 5.2, 5.2, 1.2 max.
0.950 4.4, 5.8, 1.2 max.
0.770 4.4, 5.8, 1.2 max.
0.750 4.4, 5.8, 1.2 max.
1.0
3.8, 3.8, 2.74 max.
2.2
3.3
4.7
1.35 5.2, 5.2, 1.0 max.
1.24 5.2, 5.2, 1.0 max.
1.04 5.2, 5.2, 1.0 max.
EQUATION 5-2:
V
OUT
DutyCycle = -------------
V
IN
Duty cycle represents the percentage of switch-on
time.
Sumida Corporation
®
CMD411
CMD411
CMD411
Coilcraft
®
1008PS
1812PS
1.15 5.9, 5.0, 3.81 max
EQUATION 5-3:
1-
T
ON
= DutyCycle
×
---------
F
SW
Where:
F
SW
= Switching Frequency.
The inductor ac ripple current can be calculated using
the following relationship:
5.6
5.6.1
Thermal Calculations
BUCK REGULATOR OUTPUT
(V
OUT1
)
EQUATION 5-4:
Δ
I
L
V
L
= L
×
--------
Δ
t
Where:
V
L
∆t
=
=
voltage across the inductor (V
IN
– V
OUT
)
on-time of P-channel MOSFET
The TC1303/TC1304 is available in two different 10-pin
packages (MSOP and 3x3 DFN). By calculating the
power dissipation and applying the package thermal
resistance, (θ
JA
), the junction temperature is estimated.
The maximum continuous junction temperature rating
for the TC1303/TC1304 is +125°C.
To quickly estimate the internal power dissipation for
the switching buck regulator, an empirical calculation
using measured efficiency can be used. Given the
measured efficiency (Section
the internal power dissipation is
estimated below:
Solving for
∆I
L
= yields:
EQUATION 5-5:
L
-
Δ
I
L
= -----
× Δ
t
V
L
When considering inductor ratings, the maximum DC
current rating of the inductor should be at least equal to
the maximum buck regulator load current (I
OUT1
), plus
one half of the peak-to-peak inductor ripple current (1/
2 *
ΔI
L
). The inductor DC resistance can add to the
buck converter I
2
R losses. A rating of less than 200 mΩ
is recommended. Overall efficiency will be improved by
using lower DC resistance inductors.
EQUATION 5-6:
⎛
V
OUT1
×
I
OUT1
⎞
-------------------------------------
–
(
V
OUT1
×
I
OUT1
)
= P
Dissipation
⎝
Efficiency
⎠
The first term is equal to the input power (definition of
efficiency, P
OUT
/P
IN
= Efficiency). The second term is
equal to the delivered power. The difference is internal
power dissipation. This is an estimate assuming that
most of the power lost is internal to the TC1303B.
There is some percentage of power lost in the buck
inductor, with very little loss in the input and output
capacitors.
DS21949C-page 26
©
2008 Microchip Technology Inc.
